With the recent headlines about dirty surgical instruments, and the need for monitoring the cleanliness of medical devices, especially surgical instruments, I felt this should be addressed again.
I am reminded of two sayings I have heard over and over in my 40+ years in the medical field. First, if a medical device is not clean it is not sterile. Second, I would rather have a medical device that is clean but not sterile used on me as a patient than a dirty but sterilized device.
While there is continuing debate on how clean is clean, the minimum standard is visually clean. If you can see dirt or a stain on a device, re-clean it. You first ensure you have a solid visual inspection process, and then once a stain/spot is noticed, you then identify what that stain/spot is so you can start solving the issue.
Stain on a plate of stainless steel:
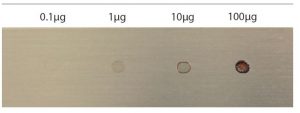
Far too many times, I have seen instruments that should never have been put in an instrument tray that have spots on them. Staff assume they're just water spots and let them go into a tray to be used. Many of the spots may be just hard water, but others could be residual protein left from the cleaning process. Regardless, they should never go into a tray and should always be sent back to be re-cleaned.
I feel your pain. I have traveled the same path of being called into a room and trying to answer questions like: "Why is this instrument dirty", "How could you allow this to happen", "If you don't solve this, your job is on the line. Fix it now!".
In my view, having a dirty instrument make its way into a surgical tray is not acceptable in today's practice. We have simple-to-use technology that can prevent this, and when used as part of a quality management system, can dramatically reduce incidences of dirty surgical instruments reaching the next patient.
I understand that solving dirty instruments is more than swabbing them, but once you can identify the stain and its source you then can start the process of fixing the issue.
For over 16 years, Healthmark has been on the forefront of helping medical facilities understand their cleaning process better. We can no longer just trust our process. We must verify the product of that process. This can only be done with quality improvement, data and products that are time tested with support to help you ensure that you are getting your instruments clean and keeping your facility out of the headlines.